Dear Rocket Fans,
Last Sunday it was finally time for our home-built long-seam welder to show its worth. The propellant tanks for Spica I had to be welded. Prior to this, of course, a lot of work has been done, both in making the long-seam weld but also in fine tuning it and finding the right settings for the highest strength. For this purpose, we prepared a series of samples that were tested for strength.
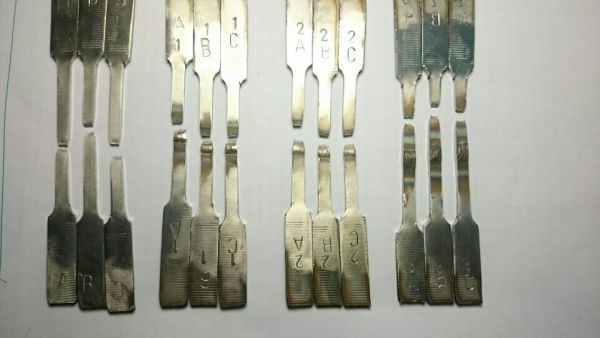
As seen there are four sets. The first is just the raw plate, so we have a basis to compare the welded items with. Next, two sets of items welded from one side and finally a set of specimens welded from both sides of the plate. The result of the tensile test is shown below.
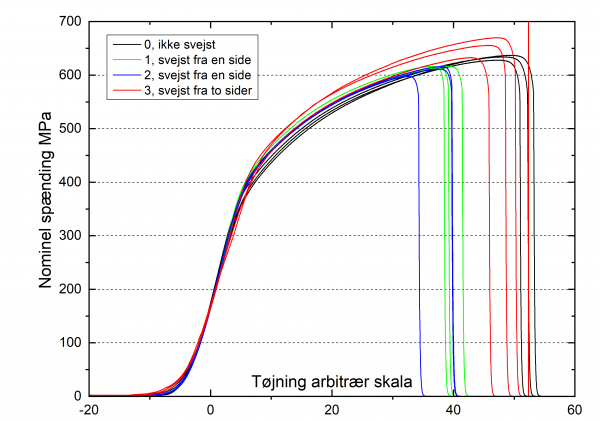
As can be seen, the base has a yield strength of about 633 MPa. The six samples welded on one side have a yield strength of about 620 MPa, so we have a welding factor of 0.98 here, quite respectable actually. Even better however, is the plate welded from both sides. There is little spread but the mean is around 652 MPa. Also note in the pictures above that the breakage does not occur in the weld, but in the piece above the weld. So with this welding technique we do not lose strength at all and thus it is easy to choose how to weld the propellant tanks Spica I. The tanks for this will of course be welded from both sides.
Our home-build long-seam welder is relatively simple. It consists of a fairly strong square profile at the bottom which gives strength and stiffness to the entire setup. On top is a copper rail where we can run passivation gas through a number of small holes. Across the copper rail there are two powerful jaws that are used to clamp the workpiece. Across the two jaws we have an adjustable linear guide that can hold a regular TIG handle. Feed is controlled with a computer.
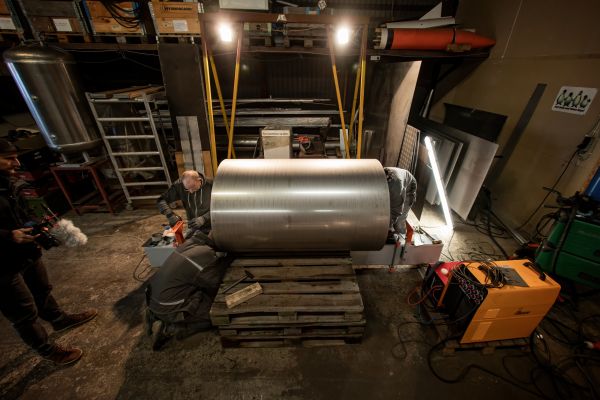
A Spica I propellant tank is made from a plate of 3000 x 1500 x 3 mm rolled to a diameter of 950 mm. It weighs around 100 kg, so it takes a little man power to get it lifted in place and tightened in the jaws, but it went without too much hassle. Next, of course, it must be aligned so that the two edges meet correctly and the TIG handle is adjusted so that the direction and height fit over the entire 1500 mm long piece.
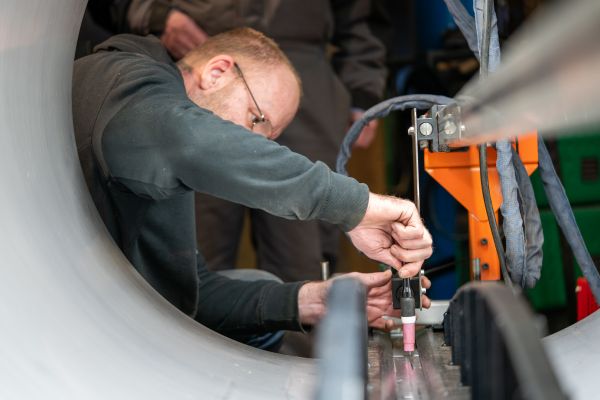
Then the ends are tagged to each other every 50 mm to ensure that everything does not warp during the long welding.

And finally we could simply press the start button and watch in awe as the 1500 mm perfect weld seam appeared.
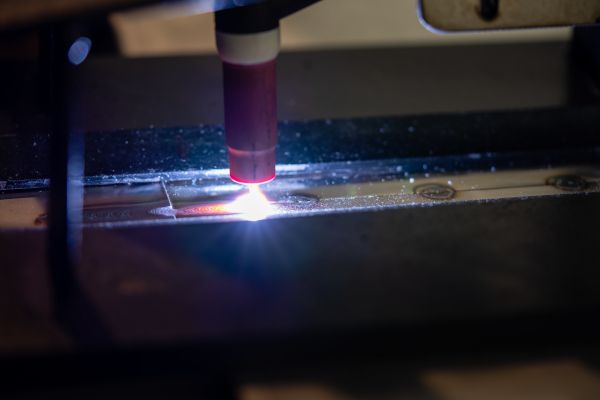
The result is quite overwhelming and not at all something we would be able to achieve with manual handheld welding, just see below.
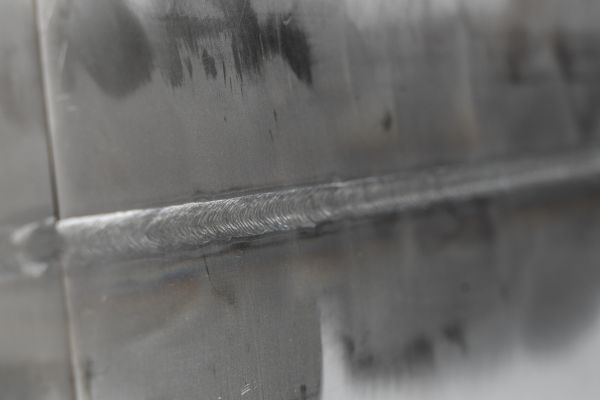
That was the inside weld of the two tanks. Next up is the outside weld. I am not too sure how our welding experts will do this but I hear rumors about propping the whole setup up on a forklift to gain the height necesarry to have the whole cylinder below the welding jig… Well, tune in next week to see more on that 🙂
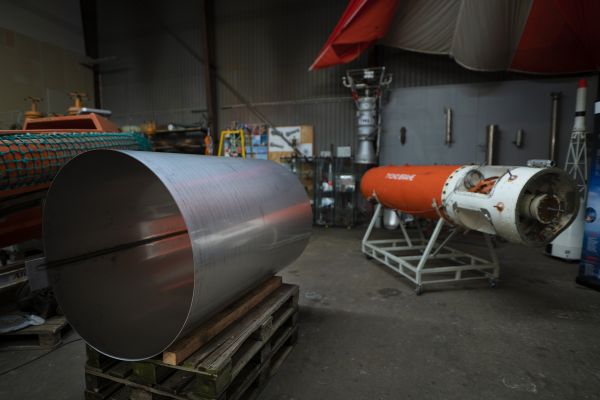
4 Comments
Comments are closed.