Dear readers
For a while now it has been very quiet from us when it comes to the progress of the capsule that is going to bring our astronaut into outer space. The reason for this is a lack of human resources for designing and developing the capsule.
We are trying to change that by gathering a small group of people who will have the capsule design as their primary focus. This means that we are beginning to transform some of the early sketches and models into something more tangible.
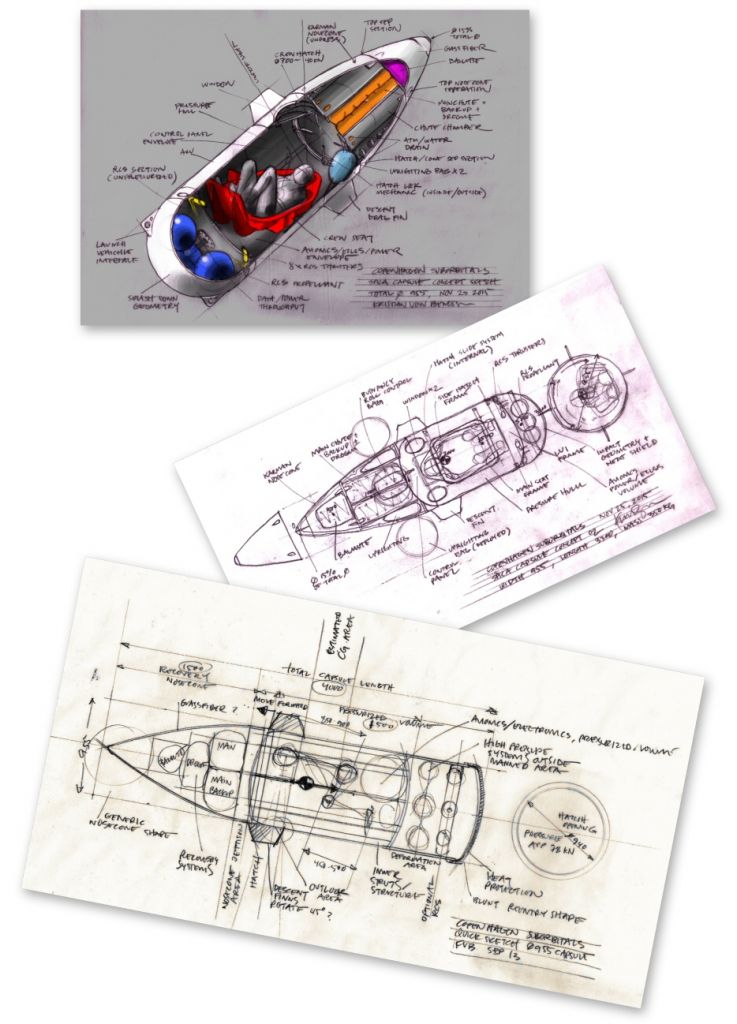
Fig. 1: Here are some of the first drawings of a design of the capsule for the Spica rocket made by
Kristian Von Bengtson
When designing a space capsule that is both safe, lightweight and actually possible for us to build, it is important to break the capsule down in sub-systems. This makes it possible to maintain the overall picture of what needs to be designed and in what order, and what influence the different systems have on each other.
Off course it is fun to go into solution mode and start detail design of little bits and pieces like safety harness mounting brackets or cup holders, but you need to maintain a view of the big picture. This is why we start by collecting all the data and results from all the work that has been done on the Spica rocket capsule these past couple of years.
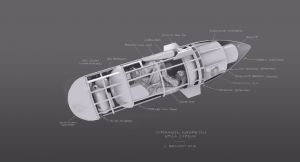
Fig. 2: A more detailed view on how the capsule might end up looking. Graphics: Carsten Brandt
We have previously worked on small scale models in free fall tests and have also had some students from the Technical University of Denmark (DTU) do a project on the ingress / egress hatch. Now we are starting full scale models.
The first will be a so called boiler plate model of the pressure hull made in steel. This is to use the same model for several tasks. It is being used to determine the location of systems that has to do with the astronaut. That would be things like seat design and –placement, hatch size and –placement, porthole size and –placement etc. Another thing that we can use a sturdy and rigid enough model to do drop tests, to evaluate different deformation structures. These will reduce the shock effect on the astronaut when the capsule has the splashdown when landing.
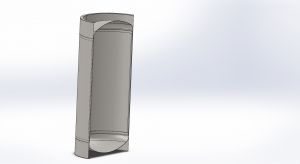
Fig. 3: This is a cross section of the boiler plate model, which we are going to weld together. Graphics.:
Martin Petersen
We are working on a budget and purchasing the materials for the capsule so we can begin building something tangible, so expect some small updates and pictures of the production of the model here on the site and on social media in the coming time.
When we are a bit further in the design process we will begin to add more of the identified systems to the boiler plate model. Here there is another advantage of using steel: it is easy to weld on and cut off new things.
It is still a bit to early to talk about the different systems. We will share that when we are a little further ahead
Ad astra
Martin H. Petersen, CS Capsule Lead
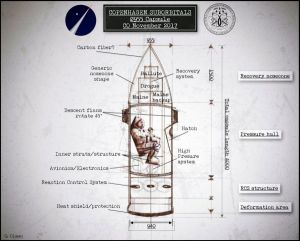
Fig.4: Kapsel grafik. Illustr.: Carsten Olsen.
13 Comments
Comments are closed.