Dear rocket fans,
As you probably remember, we decided to test coaxial swirlers in our BPM5 engine before making a full BPM100 injector. There are two main reasons for this. First, we would like to validate that the engine is actually performing as expected with these injectors. Next, and at least as important, we would like to practice the manufacture of that kind of injector on a slightly smaller scale before we move on to the very large one. It is a bit experimental and the technique must be spot on for it to work well. Let’s take a closer look at the challenges in the process.
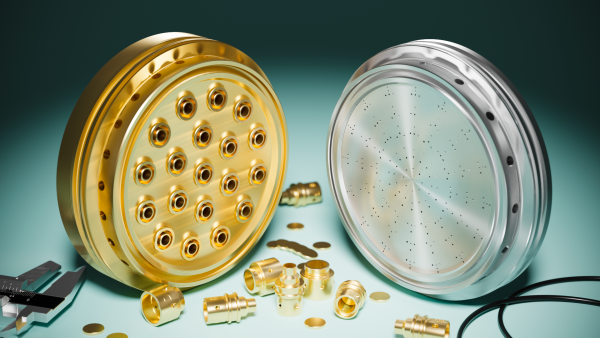
As seen in the image above, there are 19 swirlers in a BPM5 injector. These each consist of three parts that are soldered individually in one process. The picture below shows the inner and outer parts of an element. The recess in the middle of the inner part is filled with solder paste before inserting it into the outer part. In addition, the lid at the top is also put into place with a good amount of solder paste.
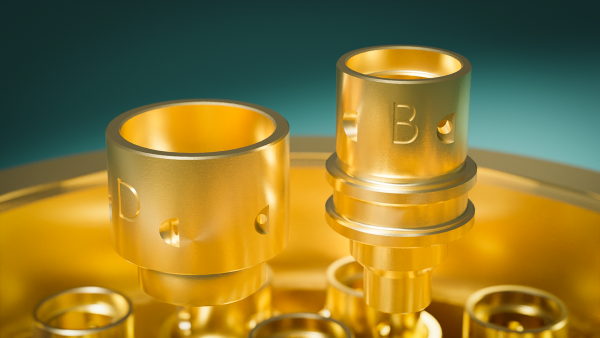
Initially, we soldered these elements in the open air with our induction heater, as seen in the image below. We have since optimized the process so that it now happens inside a glass tube filled with nitrogen. It provides a significantly nicer surface on the brass element as there is virtually no oxygen to react with the surface.
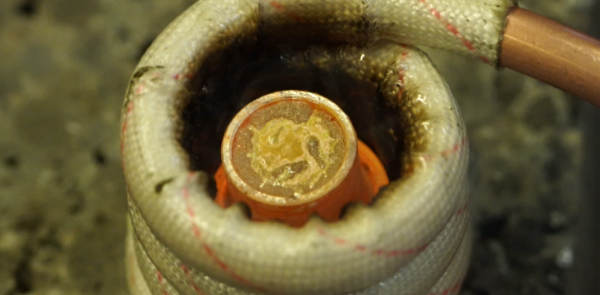
So we have good control over the individual element solder process. The difficult part is now to solder it all into one full injector assembly. Let’s take a look from the back of the entire injector to see what really needs to be soldered. In the picture below I have removed the middle plate on the left side, i.e. the plate that makes the division between LOX and ethanol (the lids at the top of the elements are also removed). This must be soldered without error to all 19 elements. Likewise, all 19 elements must be soldered to the main body of the injector. So in this injector we have 38 solder joints that all need to be perfect at the same time.
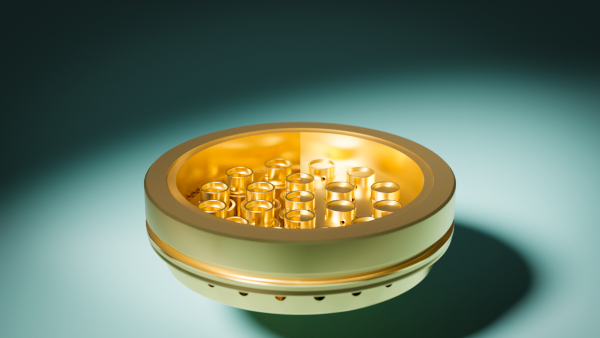
Initially, we had intended to do that soldering in our ceramic oven. However, we are a little uncertain whether we can control the temperature accurately enough. The temperature window from melting the solder paste and melting the brass itself is not very big. So instead, we have come up with a smarter plan where we do not risk heating up too much.
The idea is to make a mini retort where the injector is inside. This is then heated by adding heated nitrogen. The retort can therefore not be warmer than the nitrogen we supply and if we can control the temperature of nitrogen we can thus control the temperature of the retort. The nitrogen is taken from a 200 bar bottle and passed through a long stainless steel pipe which is resistively heated, i.e. by simply running current through it.
Our immediate estimates indicate that heating the retort and injector to just under 700 degrees will cost about 5000 standard liters of nitrogen, i.e. half a 50 liter @ 200 bar bottle. The retort is already underway, so this is something we will hopefully try one of in the coming weeks.