Dear rocket fans,
We spent quite a bit of time preparing to solder the first brass swirlers. The idea was to solder them in vacuum. For that we made a nice little stainless steel chamber that fits into our ceramic oven. At the top of the stainless chamber there is connection that allows us to pump it down to vacuum and fill it with argon instead. Placed inside the ceramic oven you can then heat it all up to the required approx. 700 degrees where the soldering happens.
The first two swirlers appear to be soldered together nicely. However, they have a lot more « patina » than we had expected when the soldering was done in argon. It’s not necessarily bad as such but now that we have the trouble with the whole vacuum soldering setup, we had hoped the result was a little nicer. You can see a bit more about the setup and the result in our latest video on swirlers that Sarunas has put together.
Vacuum brazing is a rather slow process, primarily limited by the ceramic oven which cannot withstand rapid heating and cooling. So warming up to 700 degrees and cooling down again takes half a day. Therefore, we tried something else. In our small casting workshop, where we work with casting of primary aluminum, we have a nice setup for induction heating. Jacob therefore quickly bent a copper tube of the right size to enclose a swirler and soon after we got solder paste on an element and put some heat on.
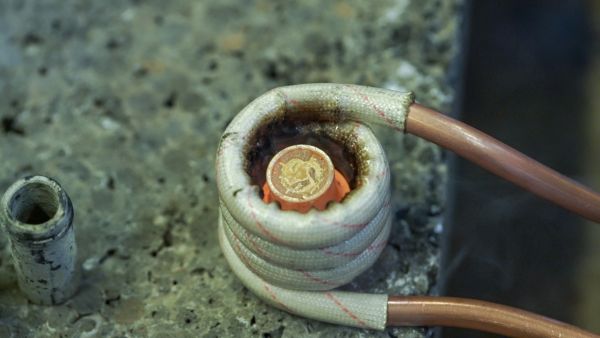
As seen in the picture (and in the video above), the element becomes briefly red-hot and the solder paste flows out and solder a total of three parts together. Compared to vacuum soldering, this takes only a minute! The element in the video is the first attempt and we can certainly succeed in getting the solder to flow a little more and a little nicer with a little optimization. But for a first attempt it looks really nice.
After soldering, the individual elements must be tested in our setup. It consists of a water tank that was previously used for BPM5 injector testing, and two pressure sensors and two flow sensors, so we can measure pressure and flow on both the oxidizer and fuel side. The other day we did not have data logging for this running yet, so it was a visual check of the spray pattern produced from the first swirlers. It looks quite promising and we look forward to characterizing the flow characteristics of the first elements. Then we have to see about the calculations behind it all hold up and whether we need to change the design.
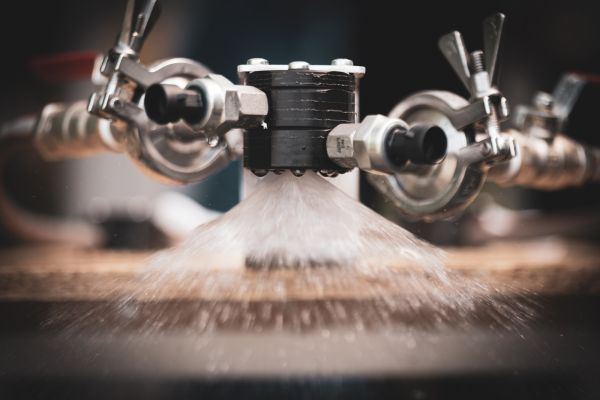
In the coming weekend we will hopefully get some data logged and then we will know much more!
5 Comments
Comments are closed.