Dear readers,
The first 100 days in the BPM-100 project has come and gone. And no, unfortunately we haven’t got a working engine here in the workshop. We’ve decided to be a little more thorough than we first anticipated.
Recognizing that swirlers are something new for us and to ensure the BPM-100 gets the best chances for success , we’ve decided to implement swirlers in an old BPM-5 engine and perform a test run with that engine, before we build the big engine. The first swirler elements are therefore designed to feed a BPM-5 engine. As you might know, it consumes 2.56 kg/s and it has to be divided into the 19 elements that have been accommodated in the new BPM-5 injector. Only the injector is changed, the rest of the BPM-5 engine is used as it is.
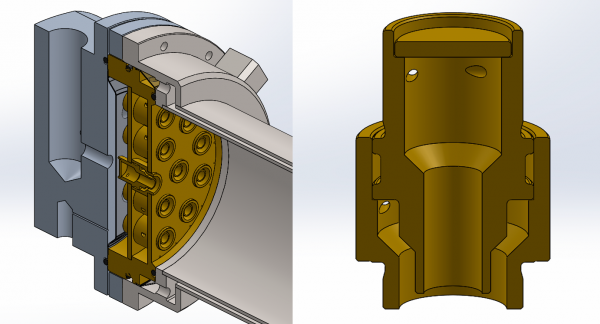
There are a few unknowns that we would like to clarify using this swirler-BPM-5. Firstly, we would like to get some experience in producing these swirlers. We get a lot of help for the primary manufacturing from PH Spaanteknik. They donates machine and man hours to help us free of charge. So the elements will be milled on one of their very nice CNC machines, it’s a great help for us and it is realistically only using CNC machining that we get the required reproducibility of the elements. So we are very grateful for the help and we hope to bring a few pictures of brass swirlers soon!
We must, however, assemble them ourselves, and here we will need some practice, they must be silver soldered together. The idea is that all elements and the entire injector is silver soldered in one go! For each element we have four soldering points. A soldering between inner and outer parts, a soldering to the small lid at the top, a soldering to the lower plate and finally a soldering to the intermediate plate that separates LOX and fuel. All of this must be prepared and soldered in one heating process, so there will be some practice needed to get it perfect.
Through static tests we will see how low injector pressure we can have while upholding a stable combustion. Our hope is that this type of injector allows a lower pressure drop than the shower head injector that we used in BPM-5.
The probably most important parameter we need to investigate through the static tests is with respect to cooling. If you look closely at the figure with the BPM-5 engine, you will see a number of small holes along the edge of the injector. It is to let fuel into the engine for film cooling. We need to determine how much film cooling is required through static testing and by measuring the fuel temperature. In a not so far future, BPM-5 will roar again and there will be new data to analyze and display.
Precise data visualization is something I have long thought we could do a little smarter, so I got access to a service called Curve. It’s a kind of a spinoff from our friends in Launcher that uses it for internal (and external) data visualization. I asked Paul from Curve to write a few lines on what Curve is:
”Curve is a tool to visualize, share and manipulate DAQ (Digital Acquisition) data in the cloud. We make it easy to share your experiment results online, either privately with your team or for a public audience. Quickly download, manipulate, and download your data to MATLAB using our plugin, or directly upload CSV & TDMS files. We are currently in free beta, head on over to the website to create an account at https://getcurve.io.”
For a start, I have tried to insert an old BPM5 dataset, so you can see it in action. It’s a little more alive in that way than the plots I usually show. If there is interest in this we might use it in the future for data visualization, take a look at it and see what you think in this dataset.
12 Comments
Florian · 24th February 2019 at 5:19 pm
Hello, i have a simple question, must the lox and fuel inlet pressure be higher than combustion chamber ? how did you achieve that with a pressure-fed cycle ? what type of gas did you using ?
best regards !!!
flo
Thomas Pedersen · 25th February 2019 at 10:46 am
Hi Florian,
Yes, it has to be higher by roughly 20% to drive the propellants into the combustion chamber. We pressurize the propellant tanks with either helium or nitrogen.
florian · 20th March 2019 at 4:19 pm
ok !! thanks for your reply, i was thinking the chamber pressure was wayyy higher than 20 bar !
I see a pressure difference between inlet and injectors, why this appens ?
A tiny rocket engine could run with only 1 or 3 of these injectors ? I mean it is possible to make a smallest working engine with one or three of these swirlers ?
is the geometry of the swirler can be modified to work good with lower pressures ? (to make water sprinkler for exemple)
Guys, your job is so interesting !!
Merci de France !
Niels · 25th February 2019 at 11:09 am
I understand you are going to test the swirlers in an old BPM-5 engine. Will the test be open for public?
Thomas Pedersen · 25th February 2019 at 8:53 pm
We will certainly try to make it public as usual. The details are however not clear yet. Stay tuned for more info 🙂
Niels · 5th March 2019 at 8:54 am
I will most certainly stay tuned and I am looking forward to spend a day with coffee, barbeque and a roaring engine
copenhagen suborbital fanboy · 11th March 2019 at 2:23 pm
i have been trying to convince my mom to donate to you guys! 🙂
https://fastcustomwritinghelp.com/blog/have-a-sunshine-on-a-cloudy-day-with-our-service · 25th February 2019 at 7:33 pm
I don’t understand much about how this works. I think that you actually have a lot of understanding in all the technological facts of this device
Mark Potter · 26th February 2019 at 2:55 am
A questionThomas, I was watching and enjoying your flight director debrief of October 3, 2018 and am wondering were you able to work out why the LOX tank did not come up to pressure as expected?
Jirka · 26th February 2019 at 9:14 am
I’d rather sit down and code for a few hours than have to rely on a proprietary service. My free software conscience’s eye is twitching.
copenhagen suborbital fanboy · 11th March 2019 at 2:24 pm
what do you mean?
Kristofers Kisiels · 10th April 2019 at 1:18 pm
What are some ways that BPM can increase the combustion chamber pressure?
Comments are closed.