Dear rocket fans,
It is a great pleasure to tell you that we have just ordered materials for the first Spica rocket! Specifically, it is materials for the first Spica rocket propellant tanks that we have ordered. Let’s take a look at the design.
We currently estimate Spica to have a lift off mass of approx. 3800 kg. For that we need two propellant tanks that can hold about 2100 kg of liquid oxygen and ethanol. With an outer diameter of 955 mm, the cylinder sections must be almost 1500 mm long on both tanks. It fits reasonably well that our roller can roll at a maximum width of 1500 mm. If we need larger tanks later they must be welded from several rolled sections. For the first tanks we start with two plates of 3000×1500 mm. They are both rolled to 955 mm diameter. As can be seen, Spica’s diameter comes in part from the size of the plates we can buy.
The first major project in this context will be a long seam welder. To ensure that the weld seam is as perfect as possible, we would like to semi-automate the process. The idea is therefore to make a setup that can hold the rolled cylinder in place while a linear guide runs a welding torch across the joint and provides as good a welding as possible. For mass optimization we need to get as close to a welding factor of 1 as possible. We have a similar setup for the round seam welding between the cylinder section and the end caps. When the tank is complete it will look like below.

Of course, it takes two more for a rocket. Piping from the top tank runs on the outside just like on Nexø I & II.
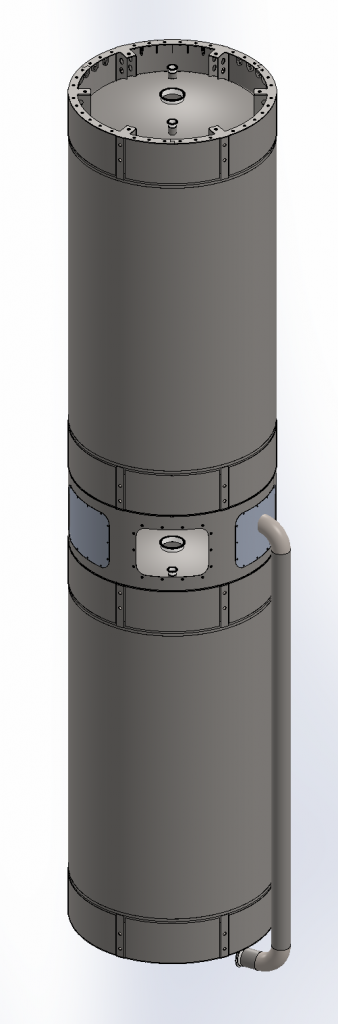
But what about the material thickness you might think? Well, we’re aiming to load the tanks hard. We have previously made experiments with smaller tanks about 260-300 mm in diameter. Here we have experimentally determined both Young’s modulus and the yield strength of 304 / 304L. We saw that the material did not start to deform until we hit about 400 MPa and the ultimate yield strength was about 900 MPa.
Spurred on by these experiments we have come up with a design where we make the tanks in 3 mm plate but with 4 mm end caps. The idea is that after manufacture, we strain harden the tanks by pushing them up above their operating pressure. We strain them so hard that they will actually deform and become significantly stronger. We expect the tank operating pressure to be around 20-21 bar and in that case probably strain harden them up to 30-32 bar. Here they will be strained a little over 500 MPa, but past experiments have shown this to be possible. The final tanks will then have slightly unusual shape for a rocket propellant tank, just see below.
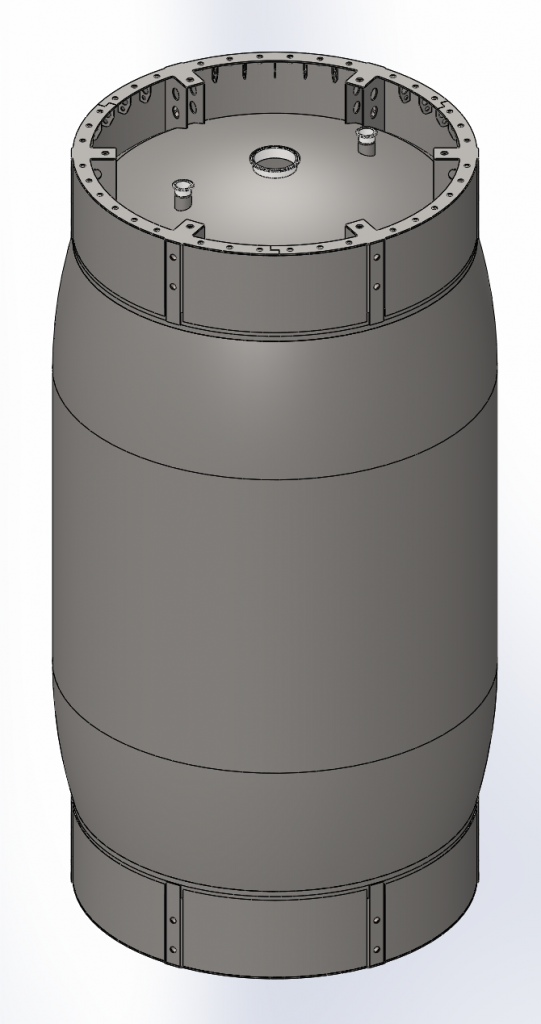
The tanks are not completely empty inside as seen below. They are equipped with anti-slosh plates along the side to prevent the liquid from sloshing from side to side. These are made in a 1 mm plate which is bent and welded to the tank wall. Notice the slot along the side that allows the tanks to deform and expand. In addition, there are also anti-vortex baffles at the bottom that prevent formation of a vortex flow towards MECO.
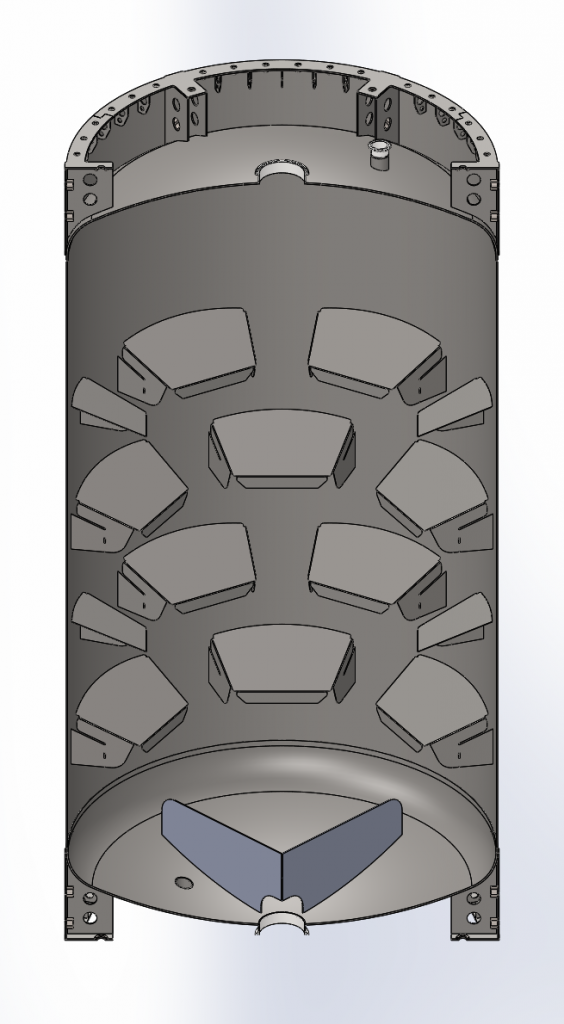
We still need to find a good deal on ø955×4 mm end caps in 304 / 304L, if anyone on the blog knows the right place to get that kind at a good price, then please let us know ASAP. Thus, we are off to a start the process (in addition to the long seam welder) by making the short intermediate piece between the two tanks, as seen below.
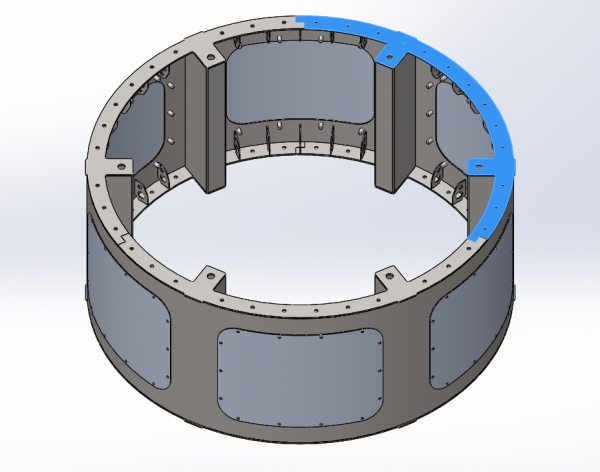
It will also be made of rolled plate but will not be pressure bearing, therefore we can weld it by hand before the long seam weld becomes operational. In addition, you will see that the flanges at the ends consist of three “rings” which are welded together. It’s something that we can make cheap and easy on our own plasma cutter.
The first materials are due already this week if everything falls into place. It will be amazing finally to weld something together that actually becomes the first Spica rocket!
6 Comments
Kasey · 9th August 2019 at 1:36 pm
What will you guys do in the event of a Rapid Unplanned Disassembly
P.S. love your guys’ work
Mads Stenfatt · 9th August 2019 at 5:27 pm
Learn from the failure and build a new and improved version.
Matt · 20th August 2019 at 6:09 pm
1. If you make a welding jig for the tanks, can you make more than 2 tanks (you know, for Spica Mk II)? Is the material very costly?
2. Also, when you weld baffles on the deformed surface, will it affect the tensile strength of the wall?
Looks like a lot of fun. Wish I could come play. Keep up the great work!
Richard Miles · 20th August 2019 at 8:21 pm
Since the strain hardened propellant tank changes the shape of the tank, will it also visually change the shape of the Spica rocket?
Jacob Jones · 27th August 2019 at 8:53 pm
Imagining a rocket with strain hardened tanks, and assuming the piping all runs along one conduit, the bulge around the interstage would probably be better covered. The additional space could be useful, but overall weight and cost are still the main concerns.
Andrew Becker · 18th September 2019 at 11:46 pm
I know a place that can do the end caps for you but I don’t know what they would charge. Email me and I will dig out the contact information when I’m at work.
Comments are closed.